Magnetic chip conveyors have become a crucial component in industries where metalworking processes produce large amounts of metal debris, such as machining, milling, and grinding. The accumulation of metal chips is a common byproduct of these processes, and efficiently managing and removing them is essential for maintaining smooth production. These metal chips, especially those created during high-speed machining, can be sharp, small, and difficult to handle using traditional conveyor systems. Magnetic chip conveyors are specifically designed to address this challenge by using magnets to attract and securely move ferrous materials, ensuring that metal debris is efficiently transported away from the workspace. This technology has proven to be invaluable in industries such as automotive manufacturing, aerospace, metal fabrication, and recycling, where the effective handling of metal waste is a key component of operational efficiency and safety.
Magnets can be embedded in or under the belt of magnetic chip conveyors. These magnets create a magnetic field that attracts and secures ferrous materials, such as metal chips, as they travel along the conveyor system. This ensures that metal shavings, even small ones, stay in place as they are transported from the machine or work area to a designated collection point. By using magnetic force, the metal shavings are prevented from falling of the conveyor. This reduces material losses and maintains the production flow. Traditional conveyor systems, on the other hand, often rely on friction to move materials, which can lead to slippage, misalignment, or clogging. Magnet conveyors reduce these risks because they provide a safer and more stable way to transport metal debris. They are especially helpful in environments that generate metal chips continuously.
Magnetic chip conveyors offer great versatility and can be customized to meet the specific needs of different industries and applications. Depending on the type of material being handled and the layout of the production facility, magnetic conveyors can be configured with flat, inclined, or curved belts. This adaptability allows them to transport materials in various directions, whether horizontally, vertically, or at an angle, making them suitable for use in facilities with complex production workflows. Additionally, magnetic conveyors can be tailored to handle metal chips of different sizes and weights. The strength of the magnets can be adjusted depending on the size of the chips being transported, allowing businesses to choose the right level of magnetic force for their needs. This level of customization ensures that magnetic chip conveyors can be integrated into a wide range of production processes, from small workshops to large-scale manufacturing plants.
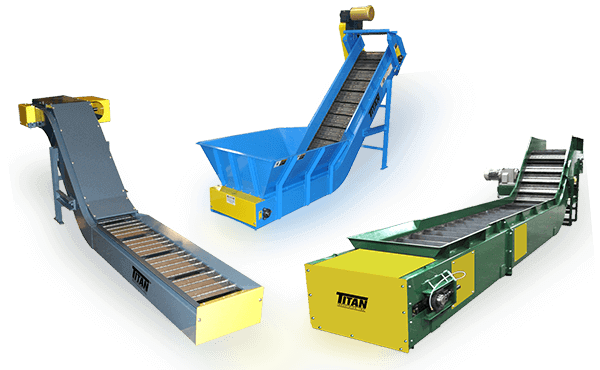
Magnetic chip conveyors are highly effective in improving operational efficiency and reducing downtime. The traditional Magnetic Chip Conveyors relies on friction in order to move the materials. This can wear out belts, components, and cause increased maintenance and repairs. Magnet conveyors operate without friction, as they use magnets to hold the chips on the belt. This reduction in friction results in less wear on the system, which means the equipment lasts longer and requires less maintenance. Magnetic conveyors also help to streamline the production process by eliminating manual handling of chips and minimising material contamination or loss. Material flow is continuous and efficient, ensuring that the production line remains operational and uninterrupted. To receive added details kindly look at Tecnimetal
Safety is a top priority in manufacturing and machining environments, and magnetic chip conveyors significantly contribute to improving workplace safety. Metal chips can be sharp and hazardous, posing risks of injury if not properly managed. In many industries, these chips accumulate on factory floors, creating tripping hazards and increasing the risk of cuts or abrasions. Metal chips that are mixed with oils and lubricants may also cause fires. Magnetic chip conveyors automate the removal and transportation of metal chips. This reduces the risk that workers will have to manually handle dangerous materials. The work environment is cleaner and safer, as workers are not exposed to sharp metal chips. The efficient removal of chips not only protects workers but also reduces the risk of accidents, which can otherwise result in costly downtime or even injuries.
Magnetic chip conveyors also offer benefits in the area of safety. Metalworking environments, especially those that involve machining, grinding, or cutting, are often hazardous due to the sharp nature of metal chips. These chips can be dangerous to workers if they accumulate around or on equipment. They could cause injury if the worker steps on them or comes into contact with it. Furthermore, in some cases, metal chips mixed with oils or lubricants can create fire hazards. By using magnetic chip conveyors, industries can automate the removal of metal chips, reducing the need for manual handling and minimizing the risks associated with metal debris. The work environment is cleaner and safer, as workers are not exposed to dangerous metal pieces. Magnetic chip conveyors improve worker safety by reducing manual work and stopping metal chips from collecting in dangerous areas.